Pin Wheels
or
a new take on the 3D Multi Generation Diamond Lamination Design
For some time now I have wanted to try this design. This ‘pin wheel’ is simple and lots of fun with one exception (a very dangerous miter cut of 67.5 degrees) which we will get into later. It is a spinoff of the Multi Generational Diamond Lamination technique demonstrated in my last post. All the basics laid out there are essential. Please do not take this post independently. Use the previous one and graduate up. As with the other it is simple but not easy. Be willing to get it wrong a couple of times before you take it to your critics.
With that in mind let’s get started…..
Oop’s, almost forgot, as with many of these projects, variations yield a wide variety of patterns and designs that are surprising and delightful to explore. As it happens, I had left over from another project some previously laminated material. A 1 by 1 Brazilian Walnut laminated with a 1/8th Brazilian Cherry and its opposite. Going into this project using these materials I felt might be a fun exploration.
You be the judge.
So let’s get back to it.
The most important aspect of this technique is without a doubt the jig. With this design you need the ability to cut at 67.5 degrees. This cut is very dangerous. Most miters go to 45 maybe 50 degrees but you need the full 67.5 to make this work and it needs to be accurate. (Also pay special attention to the vertical 90 degree angle of the blade to the bed of the saw or you will be making a shallow bowl). I feel the table saw is your best bet.
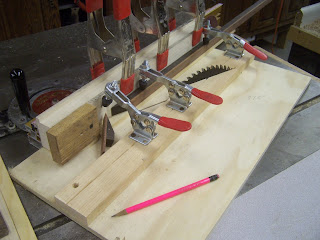
Here you can see my jig. You will have to come up with your own but be aware you will need stops on the front and rear to keep the jig from moving too far into the blade. Also keep in mind your fingers are very close to the blade so spend the time to make a jig that protects them, slides even and true. Also, be sure and stop the blade from moving before you move the material forward to load up for another cut. Nothing can move, not the material that is loaded or your cut-off. Make sure everything is clamped down tight, and be sure and count your fingers before you start and write down the number. If the number is different when you are finished you may have to go upstairs and tell your wife she was right. Humor aside, there is nothing more confidence building than the proper jig which gets you and your fingers away from the blade.
This is the goal. Nice clean half diamonds made by flipping the material for each cut.
Now we feel more comfortable and will move into the more expensive material. Notice the jig holds everything in place, even the cut-off, and uses an oak stop block so each cut-off is uniform in length. When making this jig be sure and use 3/4 inch ply for a base. I have had problems with less than that taking my material out of square simply by the force of the hold down clamps. Substitute more clamps for less pressure on them to avoid this.
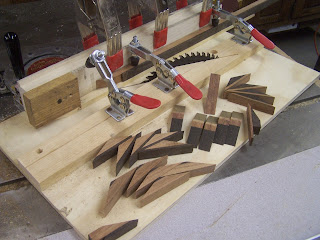
When I do my wood working lectures one of the most liberating aspects I talk about is safety. A little bit of safety goes a long way toward enjoying and having fun in your shop. The opposite is also true. If you are unsettled or unsure of your new jig or equipment – Do not use it. Just stop. Take the time to increase your confidence level by getting a friend involved or taking a course through your local wood working store. Do whatever it takes to turn this liability into an asset. Remember this is supposed to be fun, so if it isn’t, stop, reevaluate and get the help you need. You can always send me an email and I can help point you in a direction.
Here is the pinwheel pattern proper.
Here it is forming diamonds. For me, the previous post on MGDL diamond technique is safer and easier, but this one affords you the possibility of including vertical runs of laminate within the diamond. Also notice how the grain orientation is better with this 67.5 degree cut, running fully with the length of the triangle.
The different orientations and designs with these ‘half diamonds’ are also fun. I have fun with all these shapes before I commit myself to a particular look and bring out the glue bottle.
Here is another look you can get by simply sliding everything to the left or right. When I was making many backgammon boards I had lots of leftover elongated triangles so I glued them up. The more pressure I put on them the worse it got until I had glue on me the dog and a 2 foot diameter mess that sloped to the left horribly. So I let it harden up only to find one of the most curious and wonderful pieces I have ever produced. I turned it into a clock whose hands turn clockwise but the wood oriented counter-clockwise. Believe it or not the more I stare at it the more my hair grows back. Do not be afraid of making mistakes as they sometimes are the gateway to unique and wonderful creations and ideas.
Still working on ideas and patterns before glue up.
Look at these last two pictures closely and see if you can pick out the subtle differences in design.
Now we are ready to get the glue out.
When it comes to clamping these, less is always more. If you do not have a tight fit do not force it. Stress in wood is a lot like stress in people, it will find its expression like water flowing through the path of least resistance. Work on better joinery rather than forcing a bad fit. Forced fits, generally speaking, crack within the first year or so. I use a lot of rubber bands. You should not need more than that. If you do, try hose clamps, they work great. Graingers sells them in the 16 in diameter but lots of smaller ones put together also work, in some applications even better because you have multiple tightening positions around your circle rather than just one.
You will be putting together the stars in one glue up so be careful not to damage the points with your clamping. One way to protect the fine corners of the diamonds is by using caul blocks cut from scrap to distribute the clamping forces to the broad faces of the diamonds rather than the sharp points (see picture below). Also using rubber bands as clamps gives you a bumper so to speak if you choose to use other clamps. Whatever you choose be sure and keep them nice and ‘pointy’.
Then try a dry fit.
After the star we begin to add on the walnut triangles. The great thing about this project is the design possibilities are endless. You could use squares or 2 separate colors of triangles in both a horizontal or vertical orientation as you build out around your central pinwheel design.
It is important to remember you are adding as you go. If you let glue dry in the trough of the diamond it will act as an obstacle to your next fit-up. I use a tooth brush as you see here to remove any wet glue so that when it dries I have a nice fit for my next piece.
Rubber bands act as clamps for the accenting black locust triangles.
Cherry triangles on top of the walnut ones.
A close up of the pin wheel project.
So there you have it, another fun, fun, fun 3D-ish design that has many different applications. Weather a lazy Susan, cutting board, trivet, hot pad or wall decoration, it will get you lots of Oooohs and Ahhhhs through the years.
Yours in wet glue,
Steve